Design
We offer full injection mould design services based on a few different factors.
The main factors we use are mould flow analysis; projected part quantity requirements and moulding machine specifications. Mould flow analysis gives us information such as confidence of fill, part quality, fill time; air traps and weld lines. With that information, we can provide our customers with feedback to help optimise their products for mass production. It also gives us valuable information for planning runner systems, injection points/methods; part ejection position/methods; cooling circuits and venting.
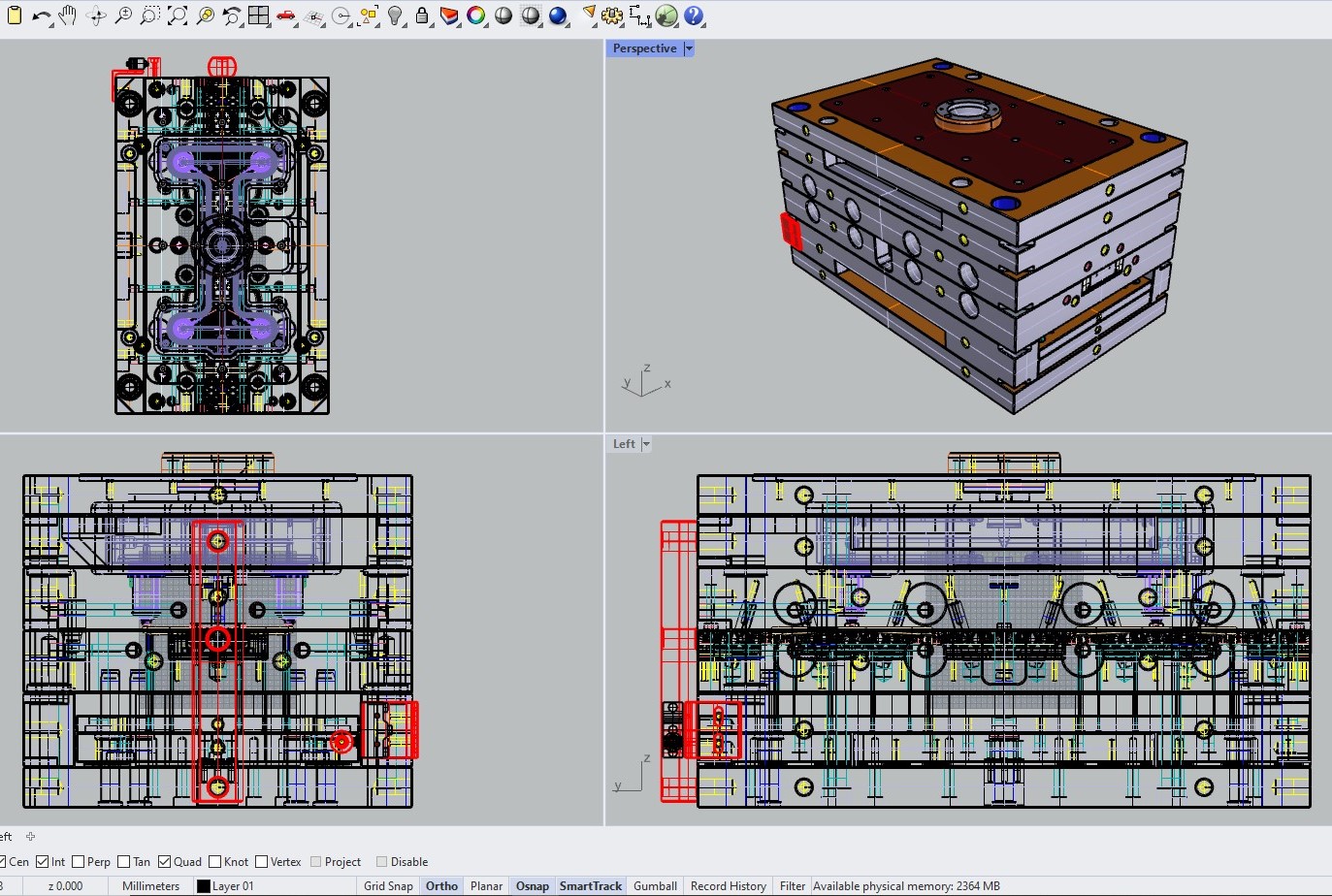